Fast injection tooling service
Rapid and short-term prototypes test market response and control costs to a great extent
- 5 injection prototype machines
- Annual output 50M+ aluminum parts
- Tolerance controllable to ± 0.01mm
- Prototype development can take as little as 7 days
TRUSTED BY OVER 1K+ COMPANIES

At XLC, we harness our seasoned expertise, robust engineering prowess, and cutting-edge technological resources to craft top-notch rapid tooling services tailored for both prototyping and small-scale production. Our holistic approach ensures that every solution we deliver is optimized for precision, efficiency, and quality, enabling you to bring your concepts to life swiftly and effectively.
Processing mold rapid prototyping
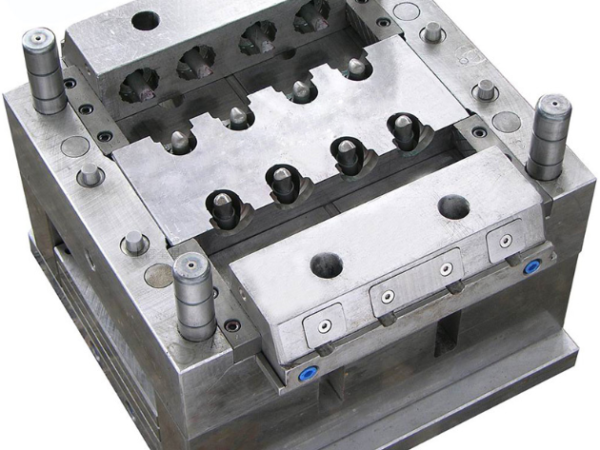
Fast Mold Making
we recognize that the key to expediting injection mold production for low-volume runs lies in utilizing machined aluminum or soft steel mold cavities. To further accelerate the process, we advocate for simplifying mold designs and incorporating stock mold components and bases. This approach not only hastens production but also maintains the integrity and precision of the final product, making it an ideal choice for businesses seeking a balance between speed and quality in their manufacturing processes.
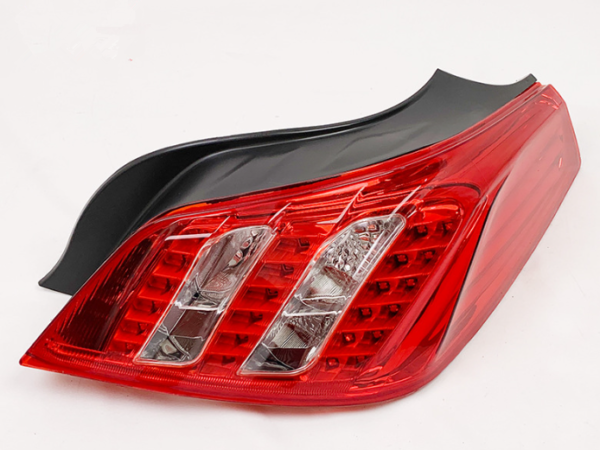
Rapid injection molding
we understand that flexibility is key in the manufacturing process. In addition to our regular production molding capabilities, we maintain a fleet of over 10 injection molding machines specifically dedicated to prototype and small-batch production. This setup ensures that your molds are promptly loaded onto the machines without any unnecessary delays, allowing for a seamless transition from design to production. Whether you're in the initial stages of product development or require a limited run of parts, our advanced machinery and experienced team are ready to meet your needs efficiently and effectively.
ISO
9001:2015 CERTIFICATED
50+
RAPID TOOLING MADE MONTHLY
10k+
PROTOTYPE MOLDINGS MADE MONTHLY
100+
THERMOPLASTICS & THERMOSETS MATERIALS
Why Choose us for Rapid Tooling?
The Top 3 Reasons:
High efficiency
leverage our in-house facilities and extensive manufacturing network to deliver rapid tooling and final moldings with remarkable speed. Our large inventory of mold components, including a variety of mold bases, combined with our advanced technology and engineering capabilities, enables us to complete your projects in just a matter of days. This streamlined approach ensures that your production timeline is significantly shortened, allowing you to bring your products to market faster and more efficiently.
Price concessions
our skilled engineers are experts at balancing cost and quality. They have a knack for smart rapid tooling design and smart material choices. For example, they might pick aluminum for its cost and speed benefits when volume is low, or steel for durability when you need long-lasting molds. This way, you get top-notch molds without breaking the bank.
high quality
prototype molds are crafted with such precision that the resulting moldings are virtually indistinguishable from those of full-scale production. They can either closely resemble the final product or achieve a perfect 1:1 match with the ultimate production standard. This means you can confidently test and refine your designs with prototype moldings that offer a true representation of the end result.
Number of devices
Spanning an expansive 2,000 square meters, our facility houses an array of rapid injection molding equipment, numbering in the dozens. This extensive setup grants us the agility to adeptly manage a spectrum of product volumes and adhere to diverse delivery schedules.
What is an injection mold
Rapid tooling, also known as prototype or bridge tooling, offers a swift and economical method for low-volume injection molding of various plastic components. Once an aluminum or steel mold is crafted via this process, it can be employed in the molding process to produce multiple part copies. This technique is particularly useful for rapidly prototyping needs within a condensed timeframe, or as a transitional step before scaling up to high-volume production.
Utilizing readily available aluminum or soft steel materials, stocked mold bases, and manually loaded inserts, rapid tooling emerges as an optimal solution for small-scale production runs. These runs are typically intended for purposes like generating marketing samples, conducting product assessments, and refining process designs.
Conventional tooling can be excessively costly for minor projects. In contrast, our bespoke rapid tooling service presents a budget-friendly, low-volume option, especially when there's no anticipation of requiring large part quantities in the future. The rapid production tooling process is frequently employed in industrial contexts for prototyping or pinpointing design flaws, offering a seamless gateway into mold making.
Here at XLC, we predominantly fabricate rapid molds through precision CNC machining and EDM techniques. However, we also occasionally incorporate additive manufacturing methods, such as leveraging 3D printing technologies, to further diversify our rapid tooling capabilities.
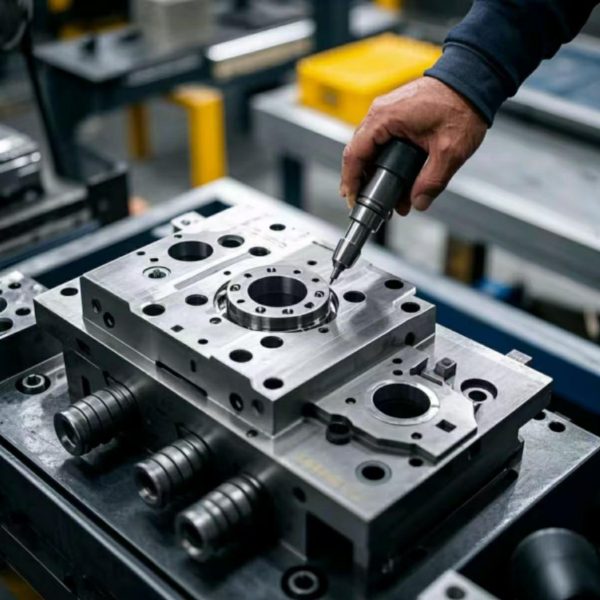
Commonly used rapid mold materials
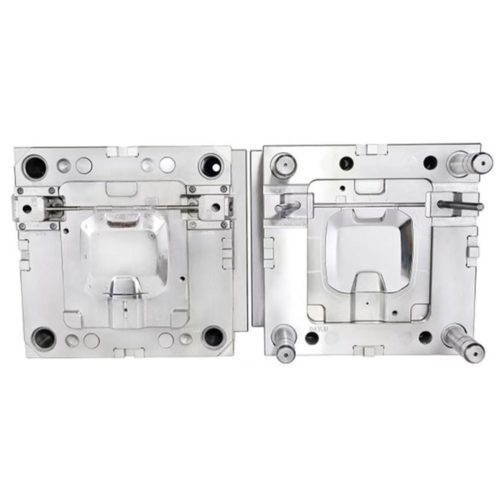
Rapid aluminum mold
For prototyping endeavors, aluminum mold tooling stands out as a budget-friendly option for producing molded components. Given aluminum's ease of machining, it can slash tooling expenses by 15–25% relative to other mold materials and pare down cycle times by up to 40%. This equates to a quicker turnaround for our clientele.
Aluminum's uniform heat dissipation ensures dimensional stability in tooling, markedly reducing deformation and minimizing waste during production. However, it's worth noting that aluminum isn't as robust as steel, which means it has a shorter lifespan and is less suited for high-volume processes.
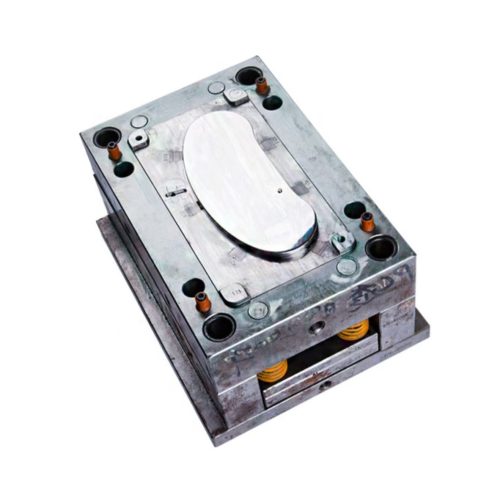
metal steel mold
Steel emerges as a robust and premium choice for tooling, yet it isn't universally applicable. Boasting a protracted lifespan compared to aluminum, steel molds are perfectly suited for large-scale manufacturing endeavors. Additionally, steel facilitates the creation of molds from high-performance engineering plastics, which exhibit remarkable resistance to wear and corrosion.
Despite its array of advantages, steel incurs higher costs than aluminum when it comes to tooling materials. The process of fabricating molds and prototypes from steel also demands a more extended period, thus necessitating a longer turnaround time.
Applications and advantages of rapid tooling
Quick production
Prototype tooling accelerates the journey from concept to creation, dramatically shrinking the gap between development and full-scale production. With this approach, you can swiftly bring your ideas to life and seamlessly move towards manufacturing, minimizing delays and maximizing efficiency.
Prototype cost
Rapid tooling is often the most economical choice for orders between 100 and 2,000 units. It's too many for 3D printing or urethane casting, but too few for costly mass production tooling. This makes it a strategic solution for moderate runs, balancing cost and volume effectively.
Material Options
Rapid tooling boasts remarkable versatility when it comes to material selection. Essentially, any material suitable for injection molding can be seamlessly utilized in rapid tooling processes. This extensive array of material choices stands as a pivotal advantage, granting clients the freedom to select the ideal material that aligns perfectly with their specific project requirements and performance expectations.
Optional surface treatment
Leveraging rapid injection molding technology, we have the capability to customize molds to achieve a variety of surface finishes, ranging from sleek and smooth to high-gloss and intricately textured. Beyond that, we offer a suite of post-molding finishing options. These include precision painting for vibrant colors, chrome plating for a reflective sheen, and silk-screening for detailed graphics and branding, allowing your molded products to not only meet functional requirements but also excel in aesthetic appeal.
Quick market test
Our rapid injection molding, with its fast production and precise tooling, boosts efficiency and speeds up market entry compared to other methods.
Workpiece cost performance
The affordability of the rapid tooling process translates into a positive impact on the bottom line for our customers.
Ready to Start Your Rapid Tooling Projects?
Rapid Tooling & Mold Making Projects
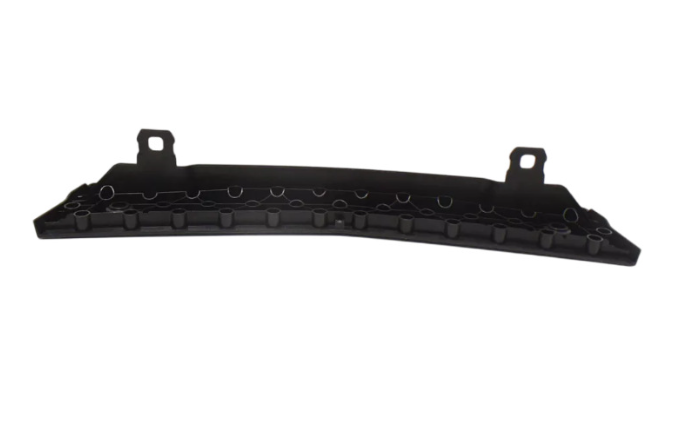
Bumper pedal project
Our client was in a bind, needing 50-100 car insurance pedal samples for testing ASAP. The catch? Production tools had an eight-month lead time and were pricey. They sought a cost-effective, quick solution for high-quality molds. This pedal project was complex, requiring us to churn out the housing, reflector, light guide, bezel, outer lens, and more, all within a tight timeframe. The assembled size was a hefty 1200x300x150 mm, and the client insisted on testing with real materials. Given the size and material requirements, 3D printing, CNC machining, and vacuum casting just wouldn't cut it. That left us with one viable path: rapid prototyping.
Rapid Tooling FAQ's
Rapid prototyping is ideal for low-volume prototypes and low-volume production. Not only can it be completed in a short time, but it can also perform functional and appearance tests in selected materials, helping you quickly verify market response while significantly reducing molding costs.
This depends on the size and geometry of the parts. For a common open and shut mold with regular size part such as 300 x 300 x 50 mm, fabrication of tools and moldings can be done within 7days.
There is no limit to material choice. Any plastics available for mass production, including common silicone and rubber materials, can also be used with the rapid tooling process.
Moldings from rapid tooling are end-use-parts quality. They are very close to mass production parts.
Normally, aluminum molds are good enough for +/- 1,000 shots, while Steel P20 molds can last for +/- 10,000 shots.
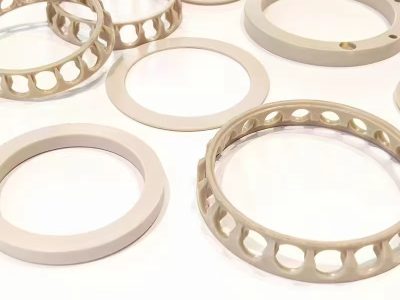
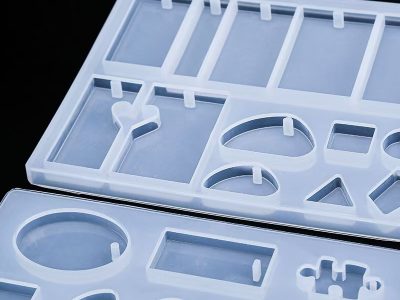
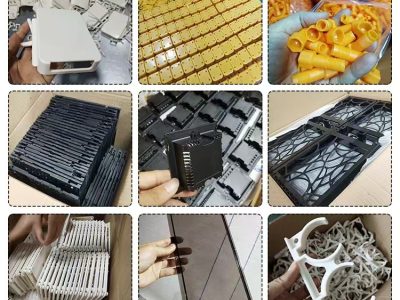
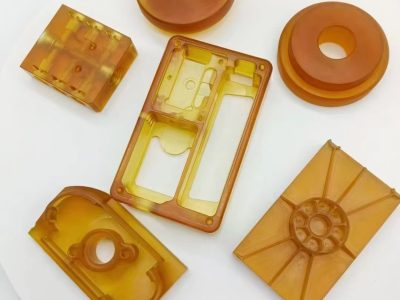
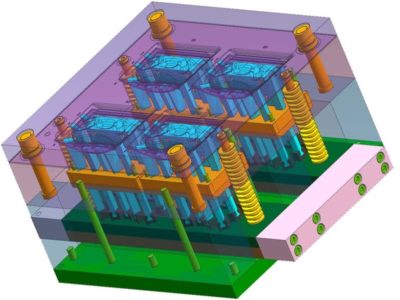
Put your parts
into production today
All information and uploads are secure and confidential.