Customized precision aluminum extrusion solution
CNC machining combined with precision refinement
- Global Delivery in 2-3 Weeks
Custom Aluminum Extrusion: Crafted with Precision
Unlike traditional extrusion companies, we have an extensive fleet of in-house CNC machines, allowing us to perform precision post-machining directly on-site. This integration ensures seamless coordination between extrusion and machining processes, resulting in higher accuracy, faster turnaround times, and superior quality control—all under one roof.
Tailored Solutions for Your Needs
We specialize in custom aluminum extrusion profiles, and our capabilities extend beyond extrusion alone. By integrating extrusion with complementary manufacturing techniques like CNC milling, turning, and bending, we can transform your extruded components into fully realized, precision-engineered parts. This holistic approach ensures that your final products meet the highest standards of quality and functionality, all while adhering to your unique specifications.
Flexible Volume Solutions
Many extrusion companies enforce high minimum order quantities (MOQs), making it difficult for clients with smaller needs. XLC breaks this mold by offering low-volume options. Whether you require a single prototype or a few hundred units, we can accommodate your needs without compromise. Our flexible approach makes us the ideal partner for projects of any size.
Rapid Turnaround Solutions
Tired of waiting over 30 days for your extrusion molds and profiles? At XLC, we shatter industry norms by delivering everything in half the standard time—or even faster! Our streamlined processes and efficient manufacturing capabilities ensure you get your components quickly, without sacrificing quality.
Plastic Extrusion Services
Our plastic extrusion capabilities cover a range of versatile thermoplastic materials, including polystyrene, nylon, polypropylene, and polyethylene. These materials are processed by heating them to a malleable state and then forcing them through a precision die under high pressure. This allows us to create a variety of shapes and profiles, tailored to your specific requirements. Whether you need complex geometries or simple sections, our plastic extrusion services ensure high-quality, consistent results.
Aluminum Extrusion Services
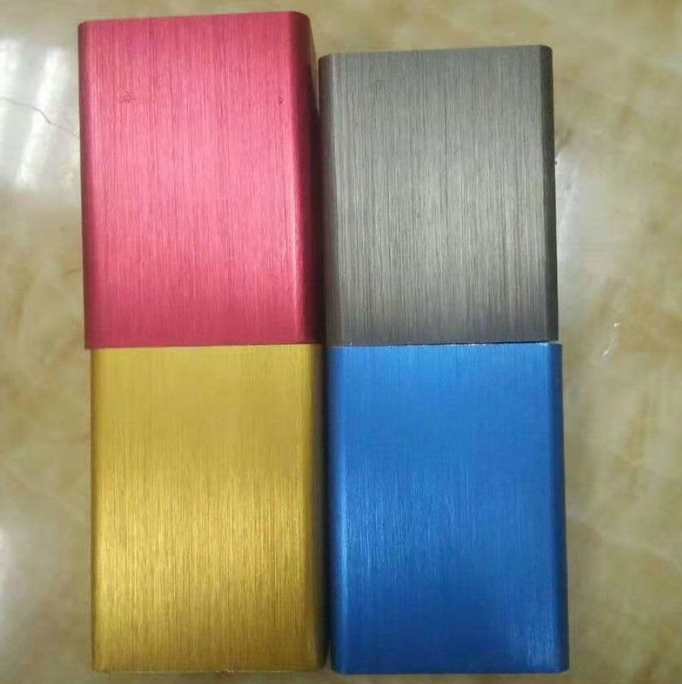
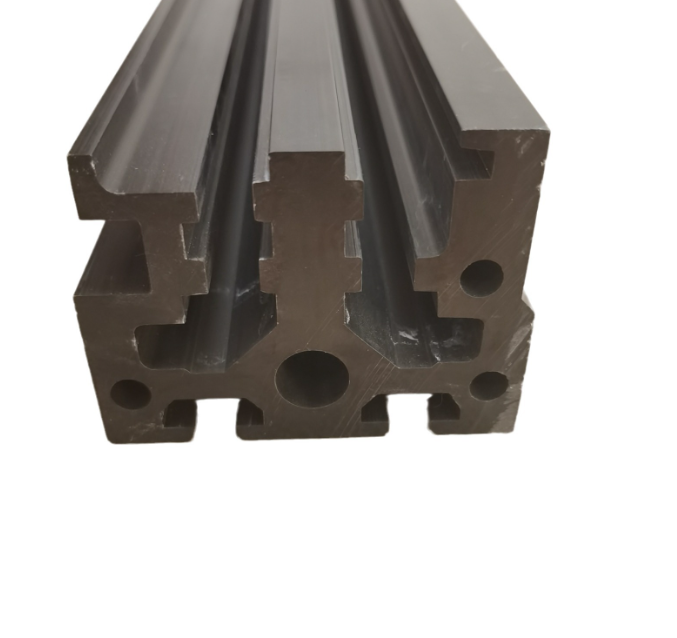
What You Need to Know About Aluminum Extrusion
Exploring the Aluminum Extrusion Process: Hot vs. Cold Methods
Aluminum extrusion is a versatile manufacturing technique that can be performed using two primary methods: hot extrusion and cold extrusion. Each method offers unique advantages depending on the desired outcome.
Hot extrusion is ideal for producing large volumes of aluminum parts quickly and efficiently. By heating the aluminum billet to a high temperature, the material becomes more malleable, allowing it to be forced through the die at lower pressures. This method is particularly useful for creating complex shapes and profiles with minimal resistance.
Cold extrusion, on the other hand, is performed at or near room temperature. This process results in mechanically superior parts with excellent surface finishes and enhanced resistance to oxidization. Cold extrusion is often preferred for applications requiring high precision and durability, as the parts produced are stronger and more dimensionally stable.
Both hot and cold extrusion methods have their place in modern manufacturing, and the choice between them depends on factors such as production volume, material properties, and the specific requirements of the final product.
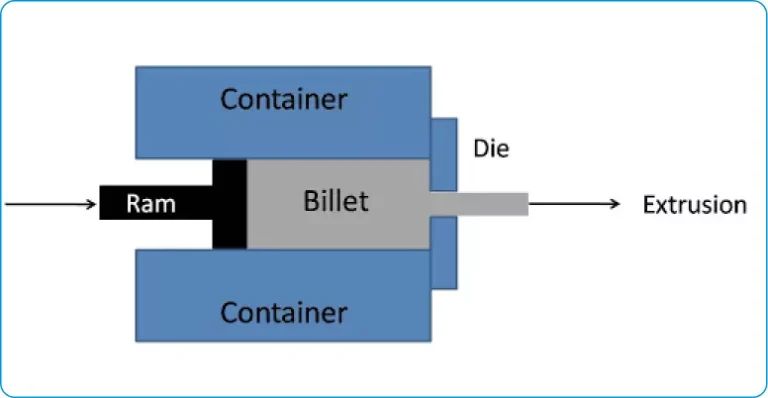
In the hot extrusion process for aluminum, the journey begins with cutting aluminum billets to the appropriate size. These billets are then heated in a furnace to temperatures ranging from 300°C to 600°C. This heating makes the metal ductile and pliable, but crucially, not molten.
Once heated, the aluminum billets are pushed into the extrusion die by a powerful ram driven by hydraulic pressure. The die can feature standard shapes like round or square apertures, or it can be custom-designed to create intricate profiles. To force the softened aluminum through the die, an immense pressure—typically around 10 million pounds—is applied.
After emerging from the die, the extruded aluminum is cooled on a cooling table. It is then cut to the desired lengths based on customer specifications. Optionally, heat treatment may be applied to enhance the aluminum’s hardness and mechanical properties.
Key Uses of Extrusion Technology
- Appliances
- Automotive
- Trains
- Construction Industry
- Medical Devices
- Display Industry
- Heatsink
- Electronics
- Automation
- Ships
While custom aluminum extrusion profiles can be tailored to virtually any 2D cross-sectional design, many projects benefit from standard shapes that are readily available and cost-effective. These include:
1.Extruded Aluminum Bar: Available in various forms such as round, square, or rectangular, aluminum bars are versatile and widely used for structural components, supports, and mechanical applications.
2.Extruded Aluminum Channel: Channels come in different configurations like U-shape, C-shape, or H-shape. They are ideal for framing, construction, and applications requiring high strength and rigidity.
3.Extruded Aluminum Tube: Available in round, square, or rectangular profiles, tubes are used for applications ranging from architectural elements to industrial piping and structural supports.
4.Extruded Aluminum Angle: These L-shaped profiles are commonly used for mounting, framing, and structural applications where right-angle support is needed.
5.Extruded Aluminum Beams: Designed for heavy-duty applications, beams provide high strength and load-bearing capabilities, making them suitable for construction and industrial use.
These standard profiles offer a balance of functionality and efficiency, making them a popular choice for a wide range of industries. Whether you need a simple bar or a complex channel, our standard aluminum extrusion profiles are designed to meet your project needs with precision and reliability.
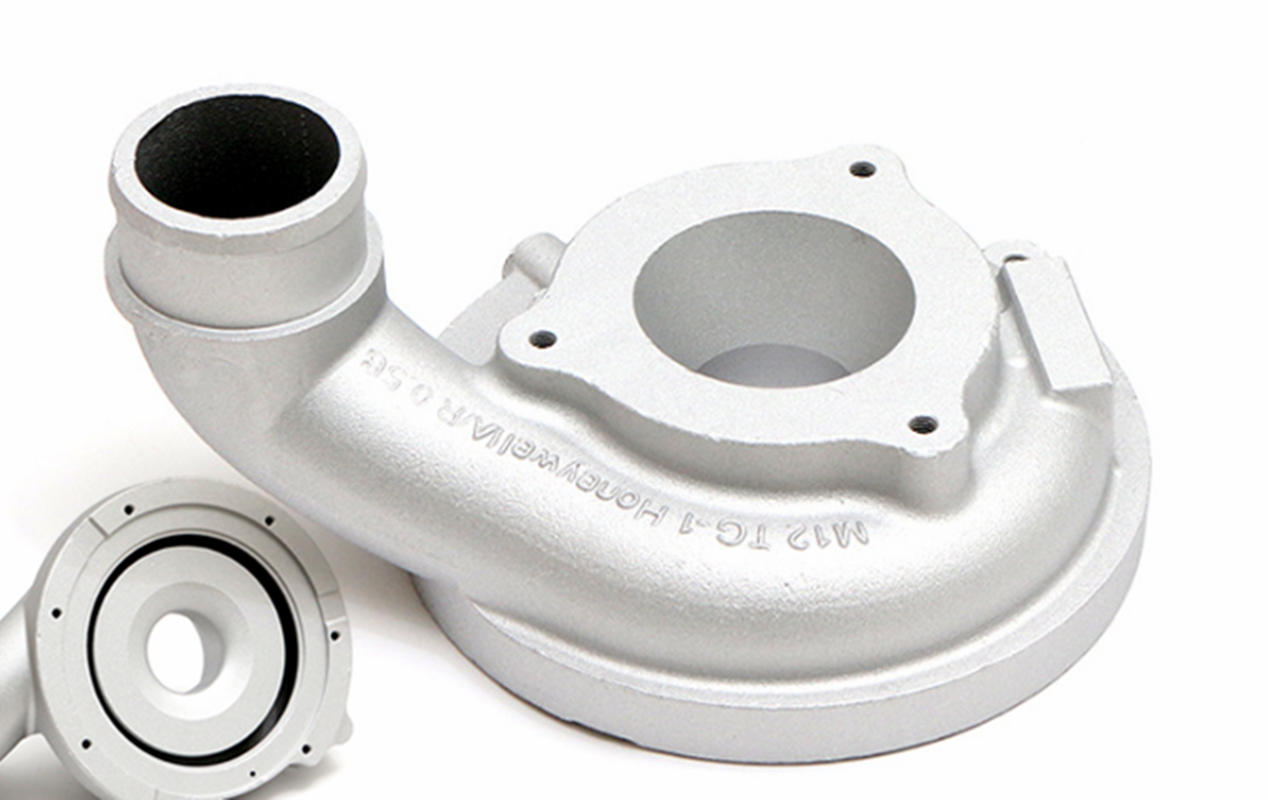
Key Standard Profile Options:
- Circular bar
- F-shape
- C-shape
- J-shape
- Square tube
- Square bar
- Circular tube
- T-shape
- L-shape
- U-shape
Thermosets
2020 aluminum extrusion (20 mm x 20 mm)
80/20 aluminum extrusion (T-slot aluminum extrusion)
2040 aluminum extrusion (20 mm x 40 mm)
3030 aluminum extrusion (30 mm x 30 mm)
Standard aluminum extrusion profiles, such as extruded aluminum channels or bars, are typically produced in large quantities by specialized extrusion companies. If your project requires a high volume of these standard profiles, working with a mass manufacturer is usually the most efficient and cost-effective approach.
However, when it comes to custom aluminum extrusion profiles with unique shapes or low-volume requirements, XLC offers a more tailored solution. We specialize in low-volume extrusion orders, making us an ideal partner for prototyping and small-batch production. Our flexibility allows you to explore custom profiles without the high minimum order quantities often required by traditional manufacturers.
Beyond creating custom aluminum extrusion profiles using bespoke dies, we also integrate extrusion with other advanced manufacturing processes, such as CNC machining. This combination enables us to produce highly customized final parts more quickly and affordably, especially when the majority of the part has a consistent cross-section. Whether you need a prototype or a small production run, XLC’s integrated approach ensures precision, efficiency, and adaptability to meet your specific needs.
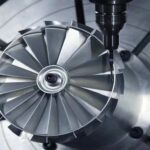
Creating a custom extrusion, then using a CNC mill to add details, holes, or threads.
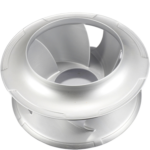
Creating a custom extrusion, then using a CNC mill to add details, holes, or threads.
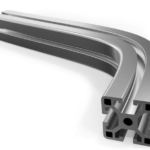
Creating a custom extrusion, then adding text or other engraving with a laser cutter.
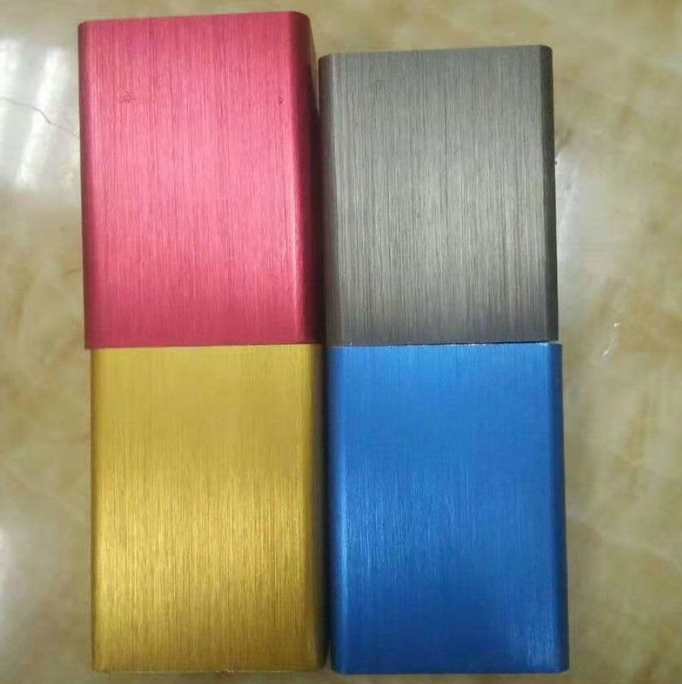
Aluminum extrusion is widely used for manufacturing functional components like tubing and frames, where the primary focus is on structural integrity rather than aesthetics. However, custom aluminum extrusion also plays a crucial role in producing high-value products that benefit from enhanced appearance, durability, and functionality through various finishing options.
When it comes to finishing aluminum extrusions, several surface treatment methods can elevate the final product. These include:
Mechanical Surface Preparation for Aluminum Extrusions
Before applying more advanced finishes, aluminum extrusions often undergo basic mechanical treatments to enhance surface quality or prepare them for subsequent processes.
Anodization Process
Anodization is an electrochemical process that enhances the surface properties of aluminum by forming a protective oxide layer. This process increases the thickness of the natural oxide layer on the aluminum surface, providing improved corrosion resistance, wear resistance, and aesthetic appeal
Aluminum Extrusions with Custom Finishes
Painting offers a versatile solution for transforming the color and surface appearance of aluminum extrusions. Whether you require a matte finish for a sleek, understated look, a glossy finish for added shine and elegance, or a textured surface for a unique tactile effect, painting can achieve the desired aesthetic. This process not only enhances the visual appeal of the extrusion but also provides an additional layer of protection against environmental factors and wear.
Why Choose Powder Coating?
For aluminum extrusions that demand both functionality and aesthetics, powder coating offers a reliable and versatile solution. It combines excellent chemical resistance with a consistent, high-quality finish, making it a suitable alternative to anodizing. Whether you need a durable protective layer or a custom-colored finish, powder coating ensures your aluminum components meet the highest standards of performance and appearance.
Why Choose Silk-Screen Printing?
For aluminum extrusions that need a touch of branding or custom text, silk-screen printing offers a straightforward and cost-effective solution. It combines affordability with durability, ensuring your designs remain visible and intact over time. Whether you need a simple logo or detailed graphics, silk-screen printing is a reliable way to enhance your aluminum products without breaking the bank.
Why Choose Laser Engraving?
For aluminum extrusions that require permanent and precise markings, laser engraving is the ideal solution. It combines high precision with long-term durability, ensuring that essential information remains clear and legible. Whether you need to add serial numbers, logos, or other critical details, laser engraving provides a reliable and lasting finish that enhances both functionality and aesthetics.
Versatile Applications of Aluminum Extrusion
Aluminum extrusion is a highly versatile manufacturing process that finds applications across a wide range of industries, including heavy industry, aerospace, automotive, consumer electronics, and even the food industry. Its lightweight nature, combined with excellent strength and corrosion resistance, makes it an ideal material for various components.
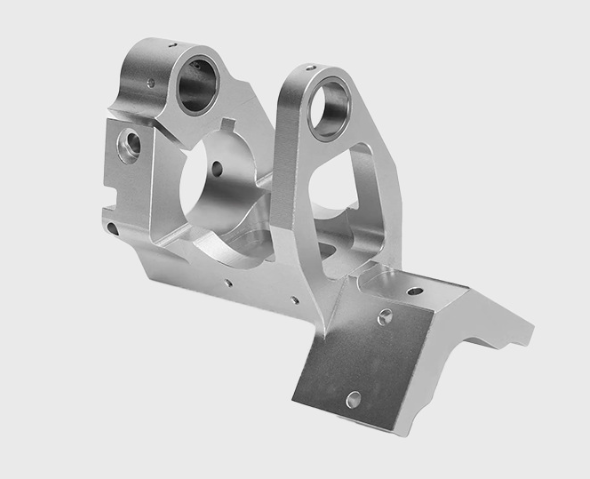
Heavy Industry and Construction
- Structural Components: Aluminum extrusions are used for beams, frames, and support structures due to their high strength-to-weight ratio.
- Fencing and Railings: Extruded aluminum profiles provide durable and aesthetically pleasing solutions for outdoor fencing and handrails.
Aerospace and Automotive
- Aircraft Components: Lightweight yet strong aluminum extrusions are used in aircraft wings, fuselage frames, and interior components to reduce overall weight and improve fuel efficiency.
- Automotive Parts: Used in vehicle frames, engine components, and interior trims, aluminum extrusions help reduce vehicle weight and enhance fuel economy.
Consumer Electronics and Appliances
- Heat Sinks: Aluminum’s excellent thermal conductivity makes extruded heatsinks ideal for cooling electronic components in computers, smartphones, and other devices.
- Enclosures and Casings: Aluminum extrusions are used for durable, lightweight casings for electronics and appliances.
Transportation and Infrastructure
- Rail Systems: Aluminum extrusions are used for train and subway components, including tracks, frames, and interior fittings.
- Marine Applications: Due to its corrosion resistance, aluminum extrusions are used in boat frames, railings, and other marine components.
Aluminum & Plastic Extrusion FAQ's
Key Advantages of Choosing XLC
- Specialized Low-Volume Expertise
XLC excels in low-volume manufacturing, ensuring that each order receives personalized attention and precision. This is particularly beneficial for startups, R&D projects, or niche applications where flexibility and customization are crucial. - Flexibility and Customization
We offer a wide range of customization options, from standard profiles to complex, bespoke designs. This flexibility allows you to experiment with different shapes and sizes without the high costs associated with large-scale production. - Reduced Risk and Cost Efficiency
Small-batch production minimizes financial risk by reducing the need for large upfront investments in inventory and equipment. This approach also allows for iterative design improvements based on customer feedback, ensuring your final product is optimized for success. - Shorter Lead Times and Faster Market Entry
By focusing on low-volume orders, XLC can deliver faster than traditional manufacturers. This rapid turnaround time helps you bring your products to market more quickly, giving you a competitive edge. - Quality and Consistency
Despite the smaller scale, XLC maintains high standards of quality and consistency. Our precision manufacturing processes ensure that each component meets your exact specifications, whether you need 10 pieces or 1,000.
Why XLC is the Right Choice
Custom Alloy Selection
Why Choose Specific Alloys?
- 6061: Known for its excellent strength, corrosion resistance, and weldability, making it ideal for structural applications.
- 6063: Offers good formability and surface finish, making it perfect for extruded profiles and architectural components.
- Other Alloys: Depending on your needs, we can source and work with other alloys like 7075 for high-strength applications or 5052 for superior corrosion resistance in marine environments.
Partnering with XLC
Our Role in the Process
Why Choose XLC as Your Partner?
- Expertise Across the Entire Process: From extrusion to post-machining, we ensure every step is handled with precision.
- Quality Assurance: Our in-house quality control ensures that every part is thoroughly inspected before it reaches you.
- Customization: We offer a wide range of post-machining options to tailor your extrusions to your exact requirements.
- Reliability: With our trusted partners and rigorous quality checks, you can trust that your order will be fulfilled on time and to the highest standard.
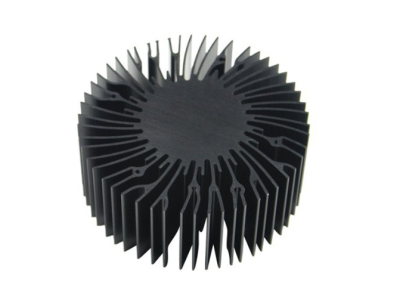
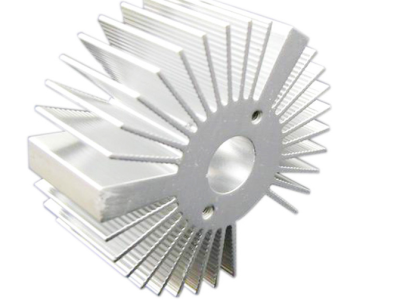
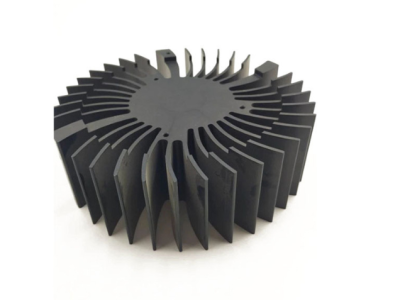
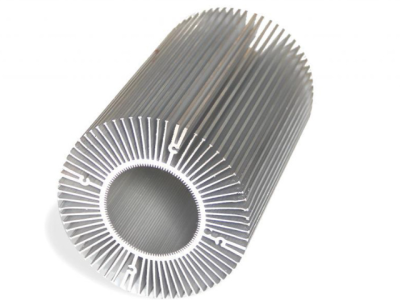
Put your parts
into production today
All information and uploads are secure and confidential.