Precision Injection Molding Services
Elevate your manufacturing process with our advanced injection molding services. We specialize in delivering high-precision custom prototype molds and production parts quickly and efficiently. Submit your design now for a complimentary quote and unlock the potential of precision manufacturing!
- 30t-1800t INJECTION MOLDING MACHINES
- 1 pc No Moq
- 10K+ injection moldings MADE MONTHLY
- 100+ PLASTIC & METAL MATERIALS
- Global Delivery
Start A New Injection Molding Quote
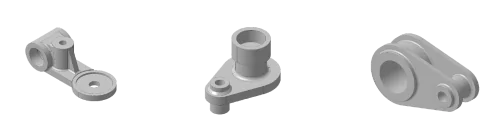
STEP STP SLDPRT IPT PRT SAT IGES IGS CATPART X_T OBJ STL files
- All uploads are secure and confidential.

What is Injection Molding?
Our Injection Molding Capabilities
At our core, we thrive on tackling the most intricate challenges in injection molding. Whether it's achieving tight tolerances, working with thin-wall designs, managing small draft angles, handling undercuts, or dealing with complex part geometries, we are fully equipped to deliver. Our expertise extends to ensuring non-defect surface finishes, maintaining dimensional accuracy, and optimizing material flow. We are committed to overcoming every obstacle to bring your vision to life, no matter how demanding the project.
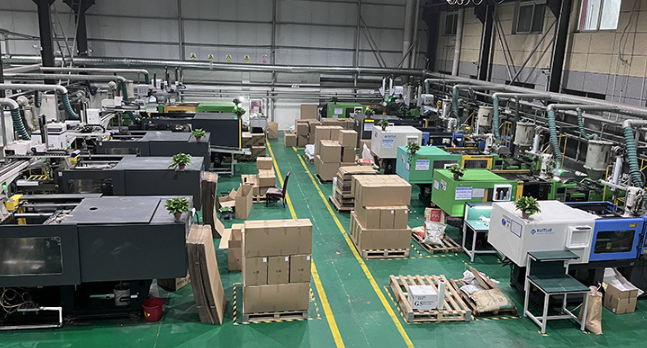
Wide range of equipment
Arrange according to order quantity. Quickly arrange global delivery

Marine products
For marine equipment shells, we take as little as 20 working days from mold opening to delivery to customers
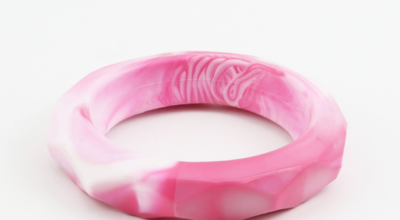
Collar
10 days to deliver customer products
Looking for Quick-Turn Molding and Parts?
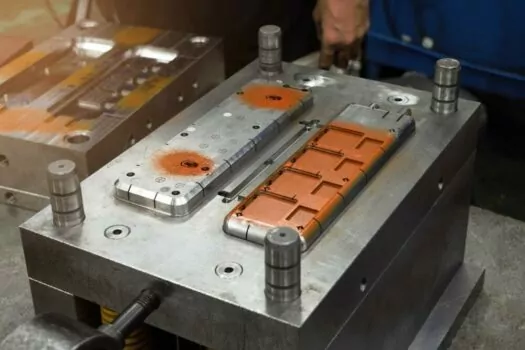
Quick-Turn Injection Molding
Get an instant quote and have your prototype parts made parts in as little as 7 business days through XLC’s ultra-fast plastic injection molding service.
Addition Injection Molding Options
Besides basic injection molding services, we also offer two variants of the process - overmolding and insert molding. Both of these can be useful in specific situations.
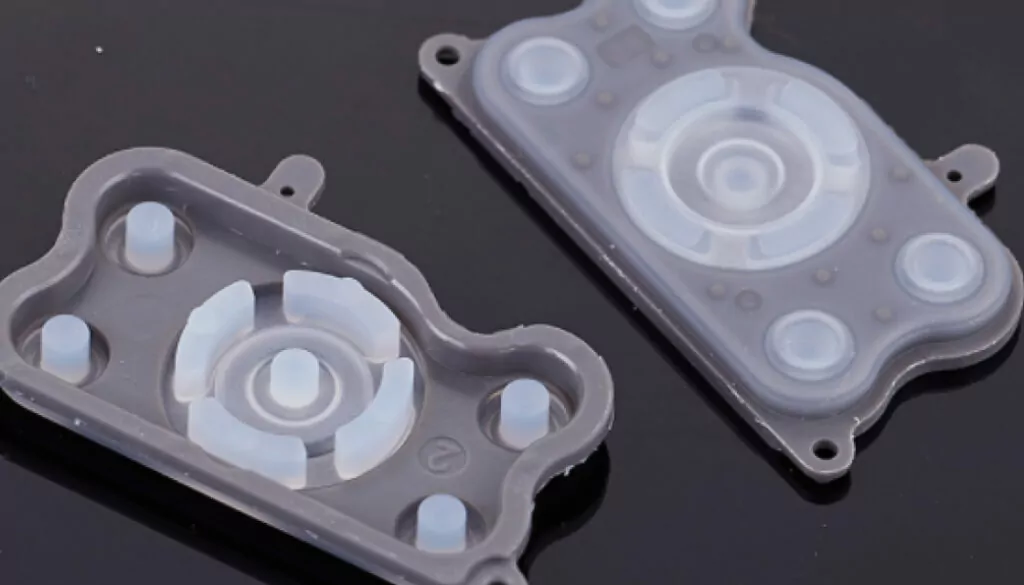
Overmolding
Overmolding uses injection molding to create a part from multiple materials. This process adds an injection molded layer of material over an existing injection molded component. The overmolding process produces chemically bonded parts made from multiple materials.
The overmolding process can be cheaper than creating and assembling components separately. The process can build layered parts from scratch or add a resistant outer layer to existing plastic parts and tools. An example overmolded product is a toothbrush with a solid plastic body and rubberized grip.
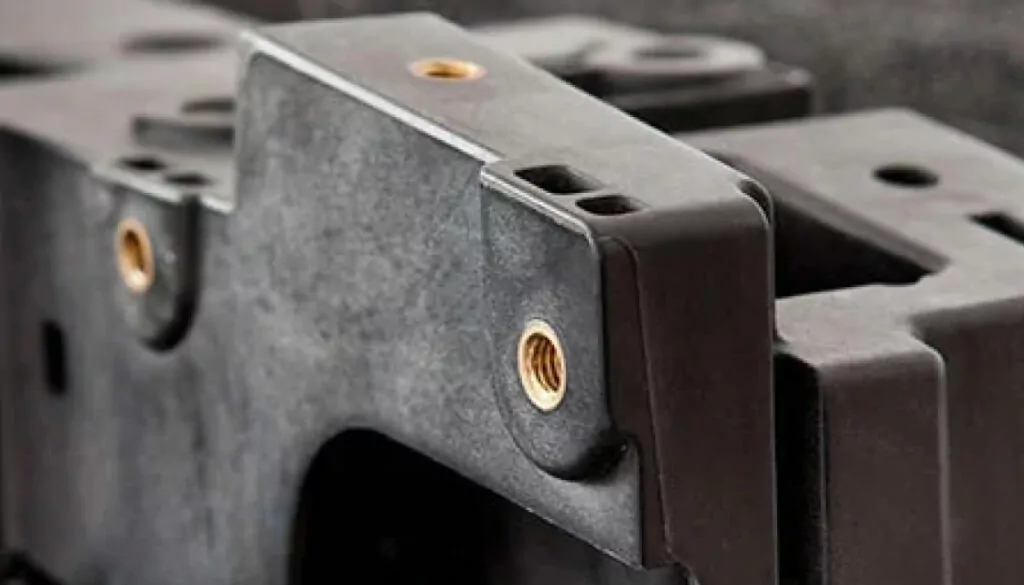
Insert Molding
Insert molding is similar to overmolding, but the substrate is not necessarily plastic and does not have to be produced via injection molding. For example, the process can be used to add a plastic coating to a pre-fabricated metal part.
Common parts made with insert molding include sharp handheld tools, such as scalpels that consist of a metal blade partially housed within a plastic handle. This manufacturing process is also frequently used to create parts with bushings, clips, and fasteners, which can be placed within the mold.
How Custom Plastic Injection Molding Works
Injection molding uses an injection molding machine made up of three sections: the injection unit, the clamping unit, and the mold or tooling. Such machines are large, expensive, and require expert operators.
During the injection molding process, plastic material in the form of small pellets or granules is fed into a large hopper. The machine moves the pellets from the hopper to a heated barrel, where they melt down into a liquid. Within the barrel, a reciprocating screw — which functions as a kind of plunger — pushes the molten plastic towards the check valve. When enough material is ready to be injected, high pressures are applied, and the material is forced into the mold through a network of channels called sprues and runners. The plastic solidifies, taking the shape of the mold cavity, and is then ejected from the mold with the aid of ejector pins. The process then repeats, with cycle times ranging from a few seconds to upwards of a minute.
When ordering custom injection molding parts from 3ERP, we will first review your design and send a quotation. When quantities and pricing have been agreed, we will quickly fabricate the tooling and, if required, send a sample molding before starting production.
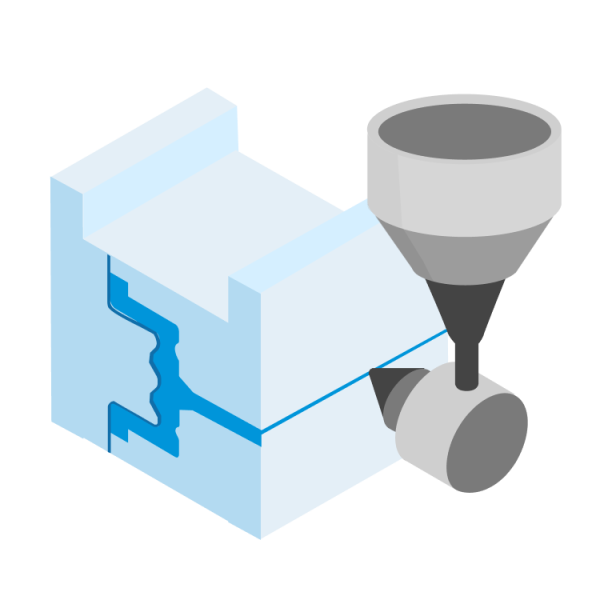
Injection Molding Materials,
Surface Finishes and More
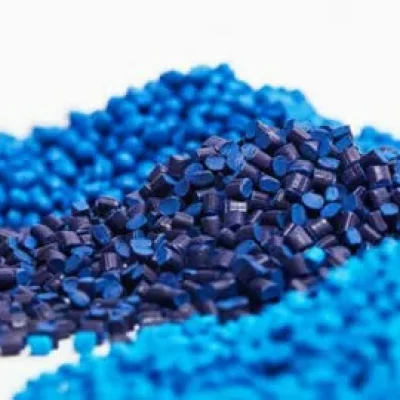
Mold Tooling and Molding Materials
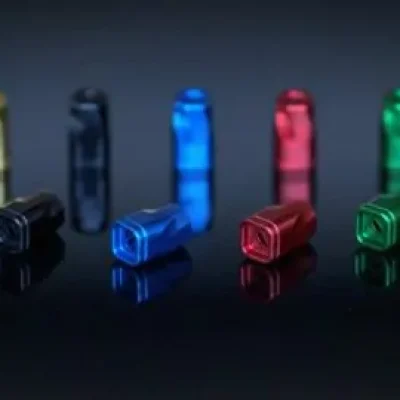
Surface Finishes
XLC offers wide variety high level surface finishes. We only list some of the common finishing options. There are more finish options for custom injection molded parts.
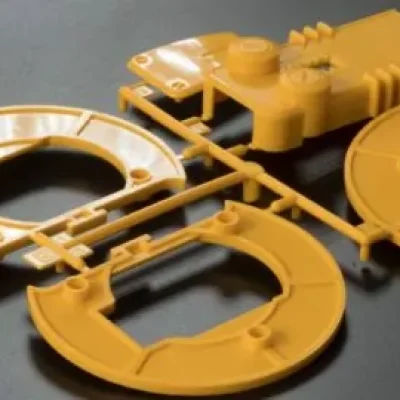
Discover More About Injection Molding
Injection Molding Applications
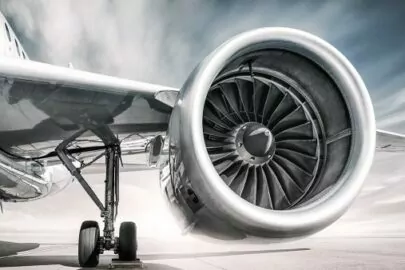
Aerospace
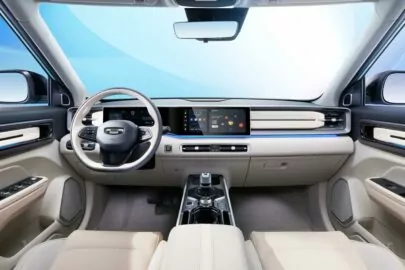
Automotive
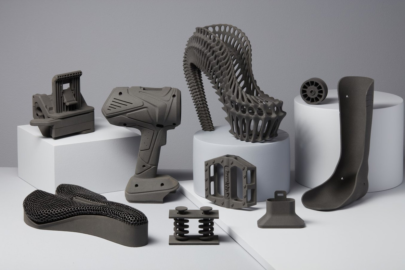
Consumer Products
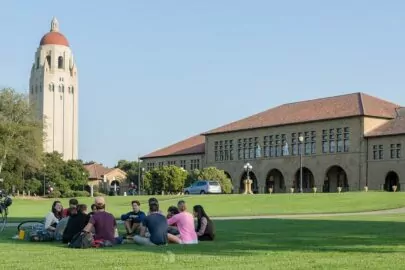
Education
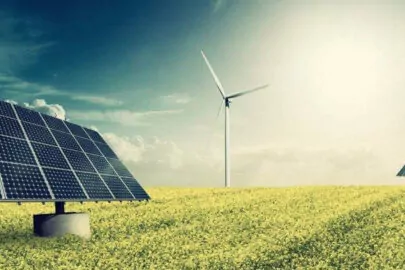
Energy
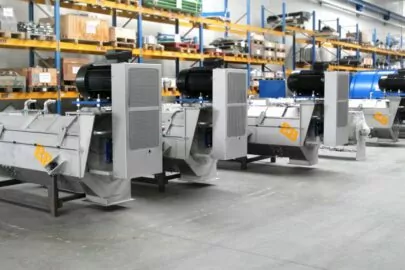
Industrial Machinery
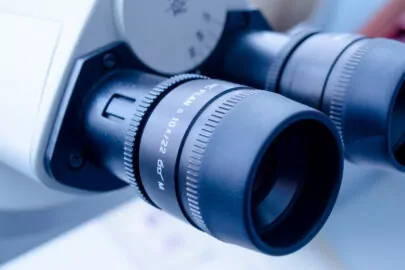
Medical
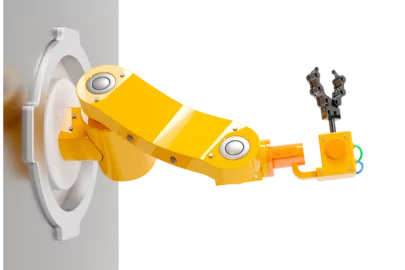
Robotics and Automations
Injection Molding FAQ's
The first step in our injection molding service is to design the injection mold tool. How long this takes will depend on the complexity of your project. The usual timeline can be as short as a week and as long as a couple of months.
The plastic pellets are melted and then inserted in liquid form into the mold tool, where it cools and takes the required shape. The process allows for high precision and tight tolerances because it can be replicated exactly each time.
Injection molding can use almost any type of plastic that can also be combined together. This unmatched versatility makes injection molding so popular and suitable for some of the most demanding industries in the world. You can check out the selection of available materials and finishes our injection molding service handles on this page.
Injection molding is one of the most affordable ways to manufacture large quantities of parts, especially for bigger production runs. Even though design for manufacturing and creating the mold can take time, the process then becomes very affordable and efficient.
Related Resources
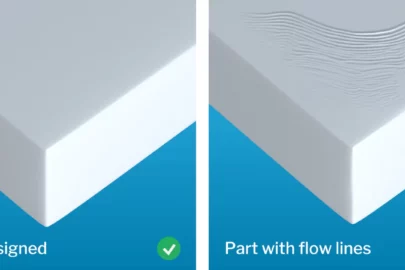
How to avoid injection molding flow lines
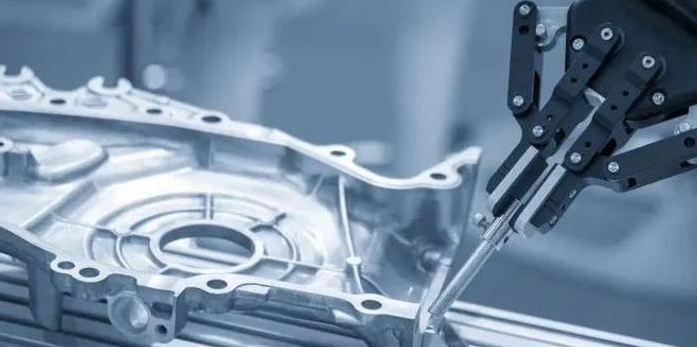
How Much Do Injection Molding Costs and How to Estimate It?
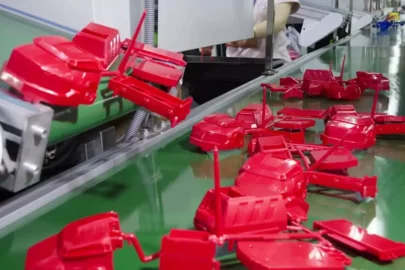
Flow Through the Details of China’s Plastic Injection Molding Process
Put your parts
into production today
All information and uploads are secure and confidential.