Customized Low-Quantity Metal Casting Solutions
From single prototype to 1000+ production parts
Metal Pouring
During our prototype deliveries to customers, we consistently encountered a recurring request: the need for low-volume metal casting services. This feedback prompted us to seek out suitable metal casting suppliers to meet this demand. However, the journey was far from smooth. Large casting companies dismissed low-volume orders as unprofitable, while smaller firms lacked the capability to meet our stringent quality standards. It was a significant challenge, but we saw it as a hidden opportunity. If we were struggling to find the right partners, we knew that overseas customers would face an even steeper uphill battle.
After two years of diligent research and strategic networking, we successfully established relationships with a select group of mid-sized casting partners. These partners not only meet our quality expectations but also align with our lead time requirements. Today, we are proud to offer high-pressure die casting in aluminum, magnesium, and zinc, as well as investment casting in brass and a full
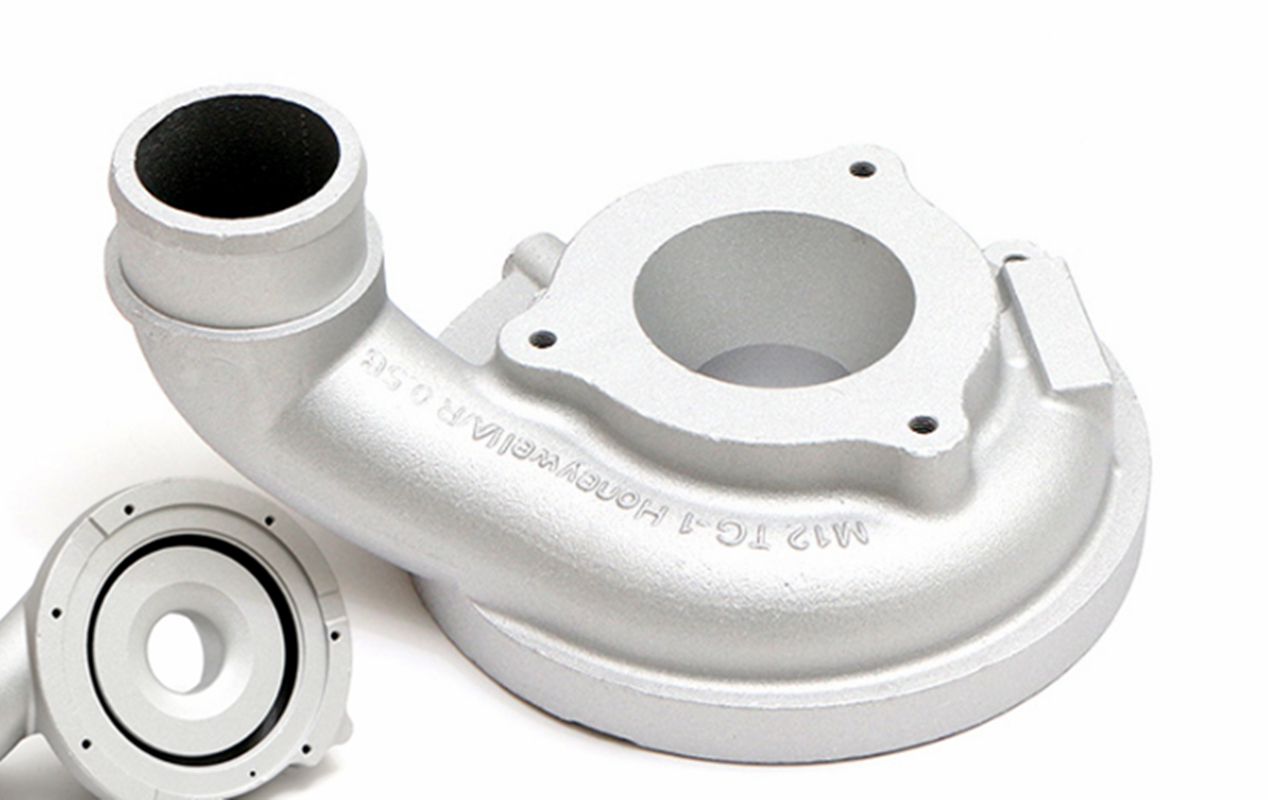
Why use XLC for Metal Casting
It might seem challenging to reach out to XLC for metal casting for the first time, but our decision is well-founded:
- Our long-standing relationships with top-tier casting partners ensure excellence in both pressure die casting and investment casting.
- Leveraging our project management expertise, we ensure seamless information flow and on-time delivery.
- Our project management ensures a smooth process from start to finish, with punctual delivery guaranteed.
Casting Materials & Finishes
- Appliances
- Zinc
- Magnesium
- Steel
- Sandblasting
- Polishing
- Plating
- Painting
- Powder coating

What is Pressure Die Casting?
A process similar to injection molding, pressure die casting is a metal casting process in which molten metal is forced into a mold cavity to create metal parts. At XLC, we use certified machines and pressure casting dies to form your designs from molten metal — typically zinc, copper, aluminum, magnesium, lead, pewter or other tin-based alloys. Our pressure die casting process is effective and very reliable, and can result in significant cost savings. Because of our flexibility, we can accommodate any project needs you may have – from small batches of 50 to as many as 1,000 pieces.
Low cost per part when carrying out a large production run
Excellent surface finish and dimensional stability
Complex geometries can be made that require little or no post-machining
Great for medium or large parts that would be slower and more expensive to machine
Metal Casting
FAQ's
XLC achieves economic feasibility in low-volume metal casting through several strategic approaches. Firstly, by optimizing material usage and minimizing waste, XLC can reduce costs significantly. Efficient material management ensures that only the necessary amount of metal alloy is used, lowering overall production expenses.
The minimum order quantity for our metal casting services is typically 10 units。
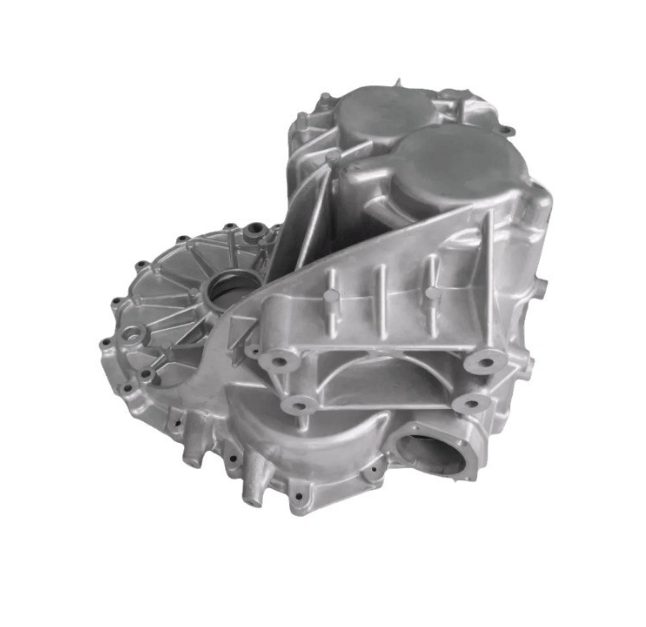
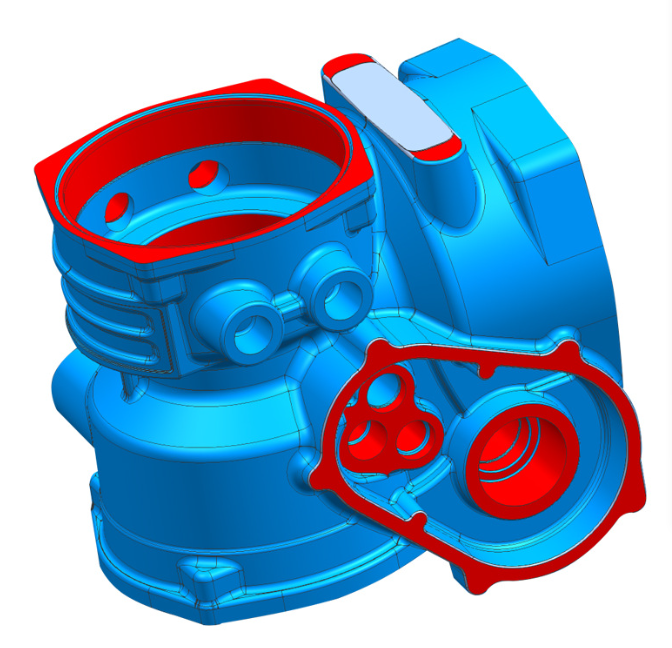
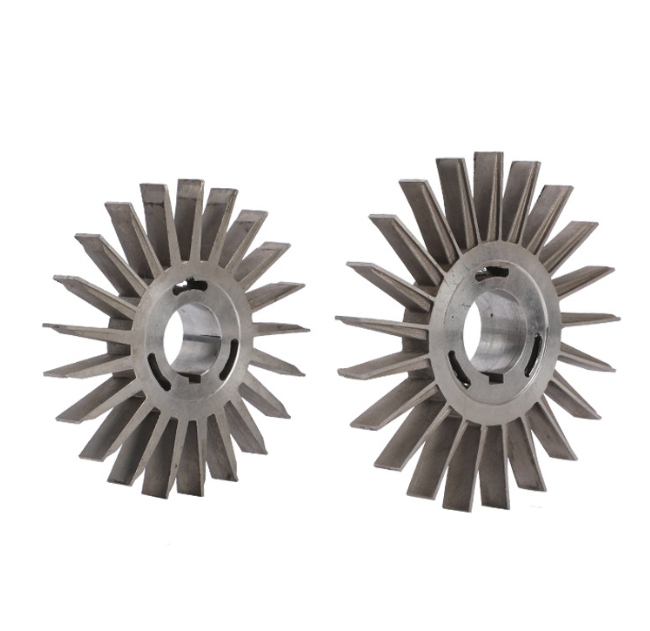
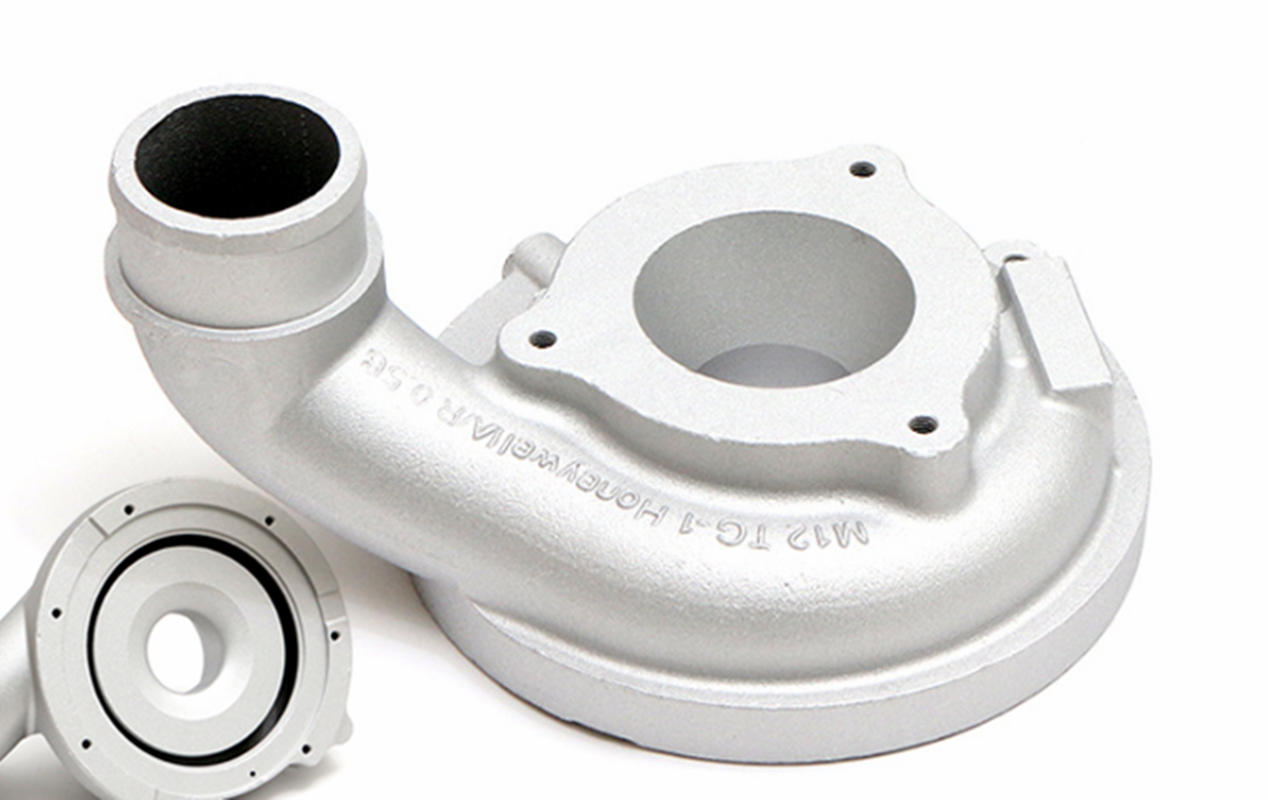
Put your parts
into production today
All information and uploads are secure and confidential.