Comprehensive Mold Making Solutions for Short-Run and Mass Production
All-In-One Mold Making Solutions for Every Project
Seeking Mold Making Supplies for Mass Production
XLC, China's Premier Mold Maker, Has You Covered
Comprehensive Mold Making Solutions for All Your Project Needs
- Plastic Injection Molds: We specialize in creating molds for both rigid plastics and rubbers, ensuring precise and durable solutions for various applications.
- Metal Injection Molds: Our expertise extends to producing molds for precision stainless steel parts, offering high accuracy and reliability.
- Pressure Die Casting Molds: We provide molds for aluminum, magnesium, and zinc, supporting efficient and high-quality casting processes.
Our advantage of making mold services
XLC's Unique Advantages in Mold Making Services:
1. Rapid DFM Reports for Proactive Quality Assurance
2. Extensive Mold Options for Seamless Project Management
3. Quick Turnaround Times
4. Integrated Molding and Production Services
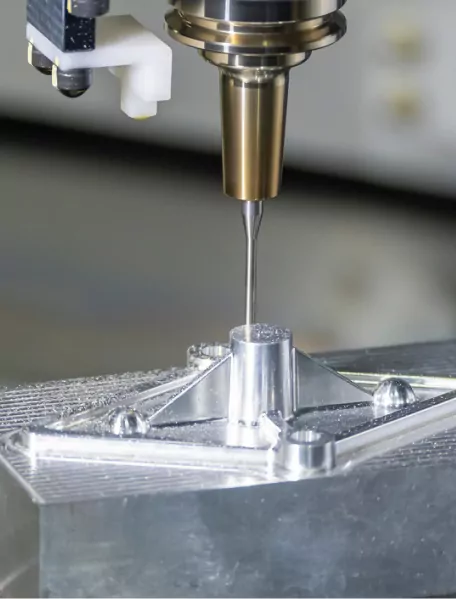
Discover Why Our Customers Choose XLC
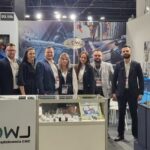
Testimonial from a Satisfied Customer
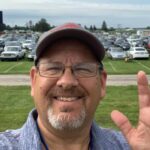
Testimonials from Satisfied Customers
“Quarterly, we order around 15 sets of precision metal brackets for our industrial equipment from XLC. Initially, we sourced these parts from a local supplier using standard machining processes. However, our contact at XLC, David, proposed using precision die casting with zinc alloy. This process not only improved the strength and consistency of the parts but also reduced our lead times significantly. The first batch had minor alignment issues, but these were swiftly addressed in the subsequent batch. Now, we save nearly 50% on production costs, and the parts meet all our quality standards. We’re very happy with the solution and the excellent customer service from XLC.”
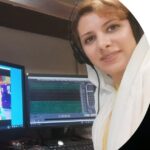
Testimonial from a Satisfied Customer
We contacted XLC Manufacturing Co., Ltd. through a supplier introduction in 2018. At the beginning, we didn't know much about the new company's trust and processing capabilities, so we had a lot of prototype tests handed over to them for development. The results showed that they were very much in line with our company's interests. Quotation, delivery and after-sales are all very good. Our cooperation with this company will reach US$3 million in 2023, and we look forward to stronger cooperation in the future.
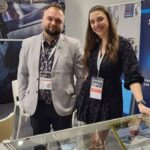
Testimonial from a Satisfied Customer
At the requirements of customers and markets, our products will invest in the market 20 days before Christmas. , For market feedback and research. Unfortunately, we negotiate with as many as 20 companies, but the results are very uncomfortable. Because of the price, delivery and other issues, there are no transactions. Under the introduction of friends, we contact XLC. They complete the mold opening, debugging and delivery on 15 working days. Our products have good feedback, and I feel that your company’s professionalism is very much
Mold Making Processes
Creating molds is a sophisticated process that demands expertise and precision. While each project has its unique requirements, a typical mold-making order generally follows these steps:
1. DFM
Once the customer confirms the mold order, we immediately begin an initial analysis of the part design to determine key elements such as the parting line and gate positions.
2. Mold design and mold flow analysis
The second step involves utilizing predictive modeling software to simulate how the molten material will flow within the mold. This allows us to identify and optimize any potential issues in the design.
3. CNC machining and EDM
We create the first set of molds using state-of-the-art machining tools, utilizing customer-specified materials like plastic, steel, aluminum, and more.
4. T1 sample
Using the newly created molds, we produce a T1 sample to provide a clear indication of how the final molded parts will appear and function, meeting the customer’s expectations.
5. Improvement if necessary
Based on the insights gained from the T1 sample, we conduct a thorough review of the mold design and implement any necessary modifications to enhance functionality and precision.
6. Commence production and shipping
We manufacture the molds in accordance with the final specifications before shipping them to the customer.
Types of Molds We are Offering
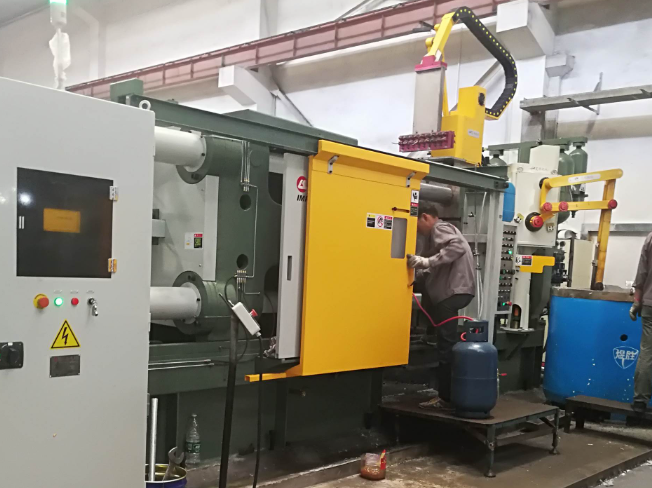
Plastic Injection Mold
Plastic injection molds are aluminum or steel molds used to make parts from a wide range of plastics, including nylons, acrylics, elastomers and reinforced materials like glass-filled polyamide. Custom plastic molds can last between 100,000 and 1,000,000 shots.
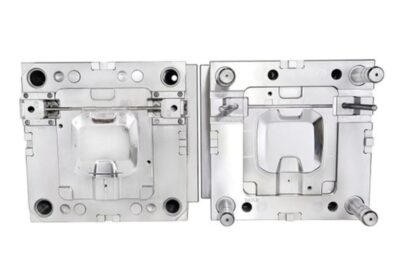
Metal Injection Mold
Metal injection molding (MIM) is a form of injection molding where a metal and binder mix is used as feedstock. A metal injection mold is usually made from tool steel to withstand the metal injection, but we can also use aluminum.
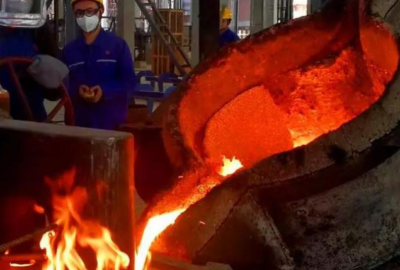
Die Casting Mold
Unlike many prototyping specialists, we can provide metal casting molds (and a low-volume casting service through our partners). These molds — typically made from hardened steel — can be used to make parts from aluminum, zinc, magnesium and other non-ferrous metals.
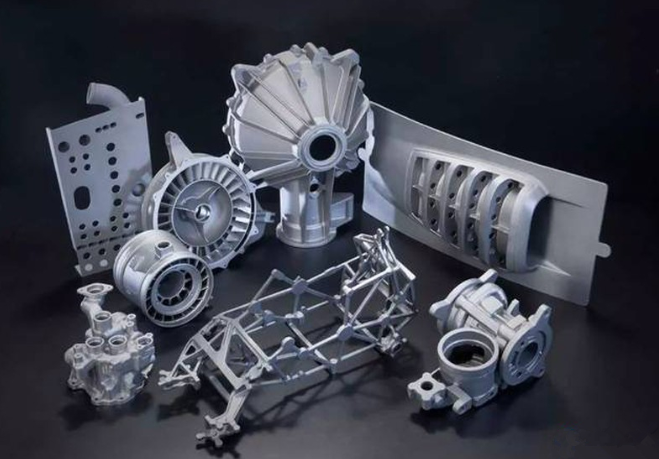
Investment Casting Mold
We can make low-cost investment casting molds by 3D printing a wax pattern and surrounding it with ceramic. The ceramic molds can then be used to make metal cast parts from metals like aluminum, zinc, magnesium, stainless steel and more.
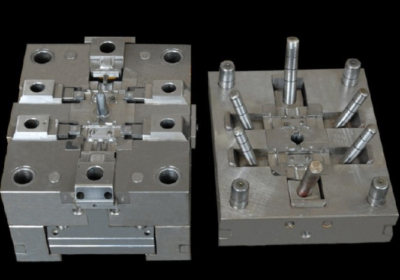
Extrusion Mold
Our metal die molds can be used for aluminum extrusions of alloys like 6061 and 6063. We also make molds for plastic extrusions of materials like polystyrene, nylon, polypropylene and polythene.
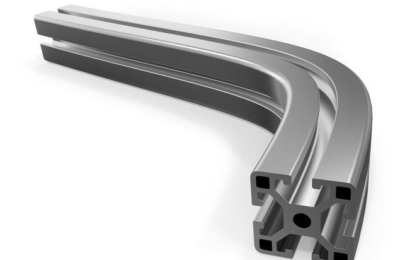
Sheet Metal Mold
Our experience making sheet metal molds for stamping and bending allows us to create sheet metal prototypes.
Mold Making Processes
XLC stands out as a leading mold making company in China, renowned for its comprehensive suite of mold solutions tailored to diverse production needs. We specialize in creating both prototype molds and production molds, catering to a wide array of manufacturing processes, including plastic injection molding, metal injection molding, high-pressure die casting, metal casting, profile extrusion, and sheet metal fabrication.
Backed by a robust team of engineers and manufacturing experts, XLC has a proven track record of excellence. We have successfully designed and produced over 5,000 molds, delivering more than 1 million parts to our global customers. Our commitment to precision, quality, and innovation ensures that every mold and part meets the highest standards, supporting your project from concept to completion.
Choose XLC for your mold making needs and experience the difference that expertise and reliability can make.
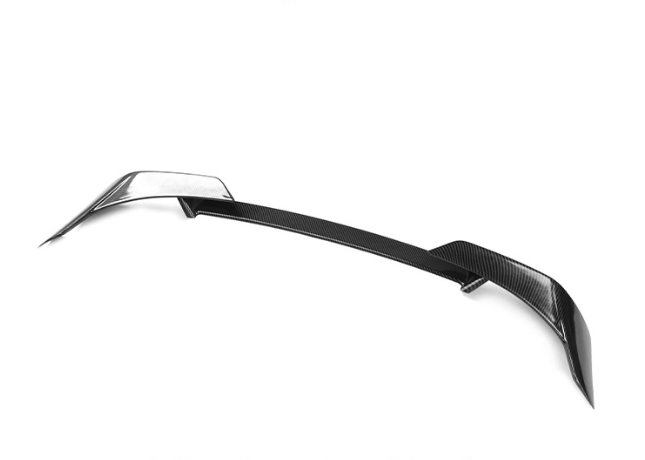
Car bumper project
We recently completed an injection molding project for a car front bumper for an automobile manufacturer. The bumper is made of PP+EPDM-T20 material, which has good elasticity and rigidity and is suitable for complex automotive exterior parts. The project required mold manufacturing to be completed in a short time to meet the customer's urgent production needs.
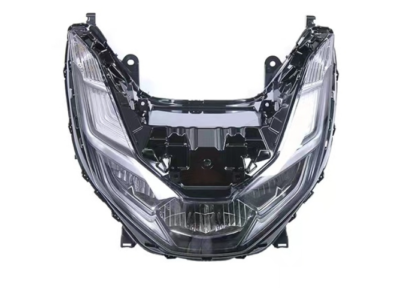
Car headlight assembly
At the customer's request, we completed the mold opening, polishing and surface treatment of the car headlight assembly within 15 working days, and finally completed the customer's order, which was well received by the customer.
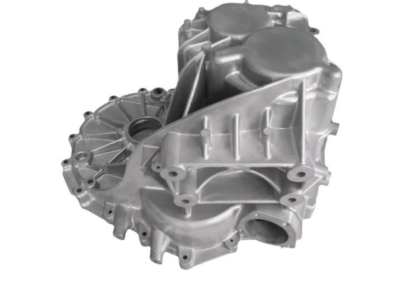
New energy cover
Within 25 days, we cooperate with new energy vehicle manufacturers to develop accessories. Promote the launch and test of new brand cars.
Mold Making FAQ's
- High Production Volume: When you need to manufacture large quantities of products consistently and efficiently, a full automatic mold can significantly reduce production time and increase throughput。
- Complex and Consistent Quality Requirements: For products that require high precision and consistent quality, such as in semiconductor manufacturing or precision plastic parts, full automatic molds can minimize human errors and ensure uniformity。
- Cost Efficiency in Long-Run Production: Although the initial investment might be higher, full automatic molds can lower unit costs over time by reducing labor and operational costs, especially in large-scale production。
- Reduced Production Cycle Time: Full automatic molds can streamline the production process, reducing cycle times and improving overall factory efficiency。
- Advanced Manufacturing Integration: If your production process involves complex workflows or requires integration with other automated systems, a full automatic mold can be part of a comprehensive solution to optimize manufacturing。
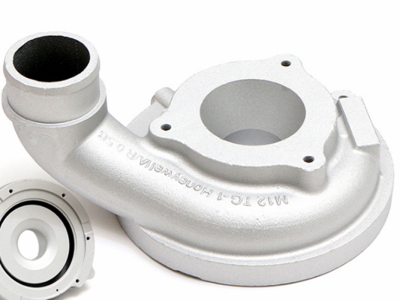
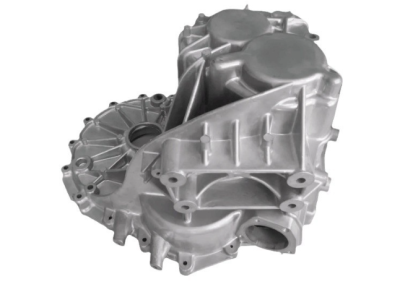
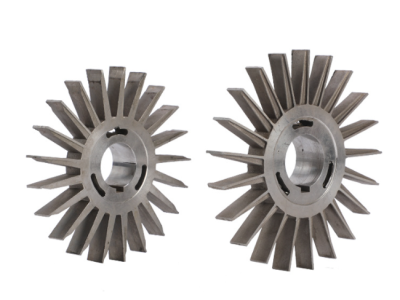
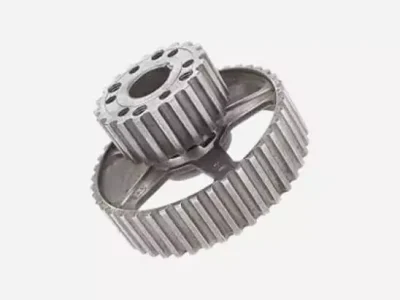
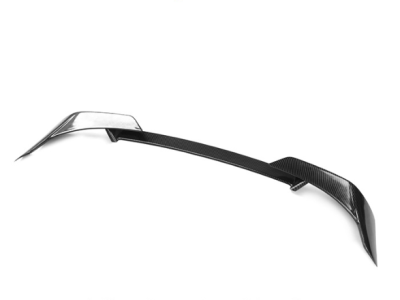
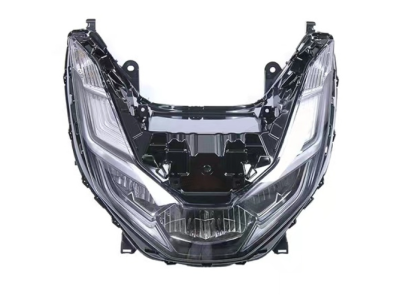
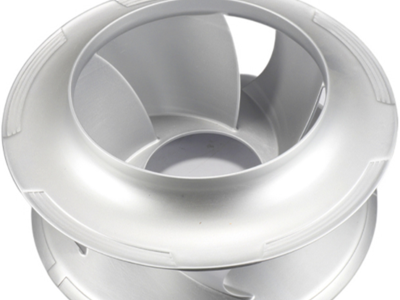
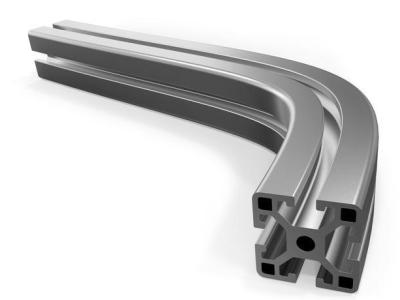
Put your parts
into production today
All information and uploads are secure and confidential.