Vacuum Casting Services & From Prototype to Production
Urethane Casting
Vacuum casting is a great method to make rigid or flexible parts, and is ideal for high quality prototypes, function testing, concept proofing and display demos. Urethane casting parts can be made from a few to hundreds as required.
Contact us today for more information about our casting services.
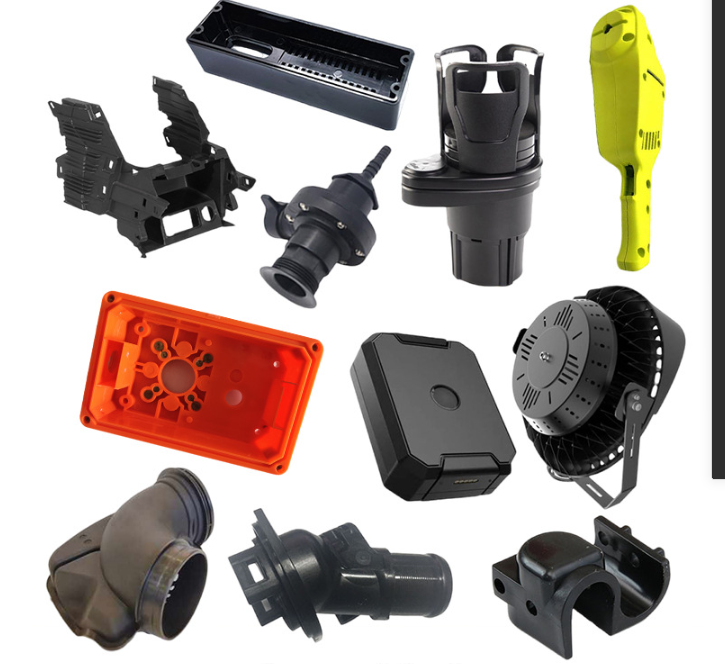
1. Rapid Production
2. Economical Choice
3. Suitable for Large Components
4. Superior Surface Quality vs. Injection Molding
5. Custom Color Solutions
6. Reliable Repeatability
Common Vacuum Casting Applications
- Visual prototypes
- Concept proofs
- Cases and covers
- Low-volume production
- Market testing
- Investor pitches
- Trade shows
What is Vacuum Casting?
Vacuum casting is a precision manufacturing technique that leverages vacuum pressure to draw liquid casting material into a mold cavity. Unlike injection molding, which forces molten material into a mold using mechanical pressure, vacuum casting relies on a vacuum to create a smooth and bubble-free surface.
This process is especially advantageous for parts with complex geometries, undercuts, or fine details. It begins with a master model, which XLC typically creates using advanced CNC machining centers (though 3D printing is also an option). This master model is then submerged in liquid silicone, which is allowed to cure and harden to form the mold.
Once the master model is removed from the cured silicone, the mold is ready for use. Casting resin is poured into the mold, and a vacuum is applied to eliminate air bubbles and ensure a flawless finish. The resin is then cured in an oven, and the finished part is carefully removed once cooled. The silicone mold can be reused approximately 20 times, making it highly efficient for small-scale production.
Each cast part is an exact replica of the original master model, making vacuum casting an ideal solution for rapid prototyping and producing small batches of high-quality parts.
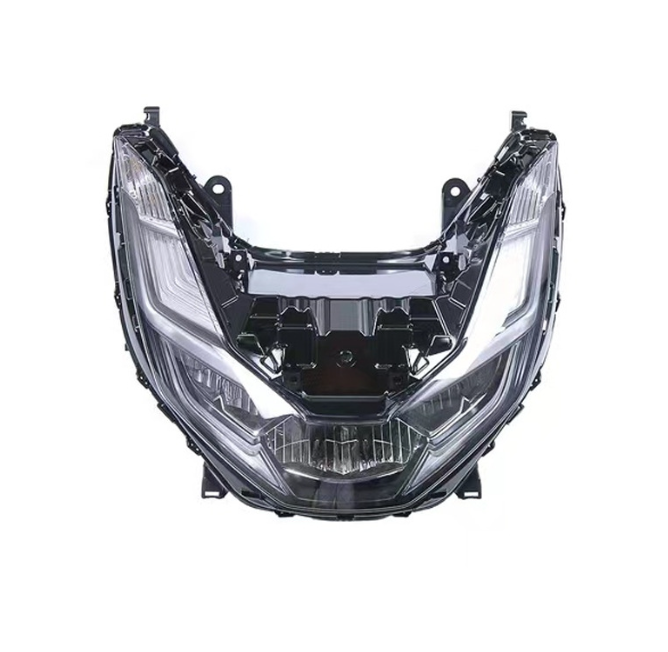
Urethane Casting FAQ's
Urethane casting is a more affordable alternative to IM, especially in low volumes. It also offers unique advantages like an excellent surface finish.
Urethane casting is best for making visually impressive prototypes, but it can also be used for non-mechanical end-use parts like cases and covers.
The silicone molds used in urethane casting have a short lifespan, typically around 20 moldings, so we dispose of them after use.
If you wish to keep the 3D printed or CNC machined master model, talk to us directly.
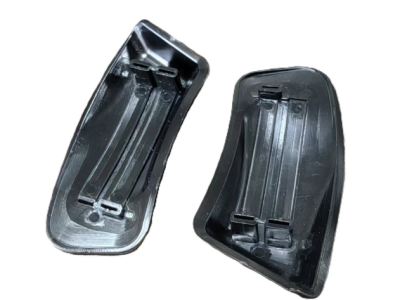
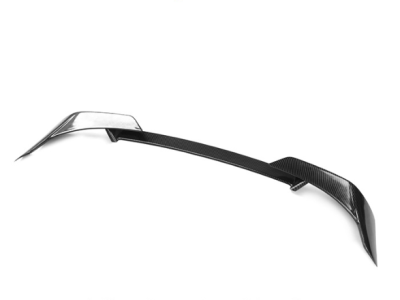
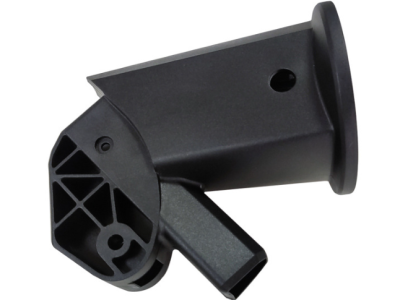
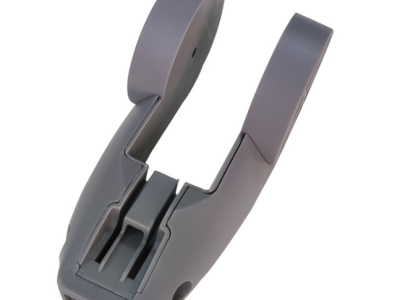
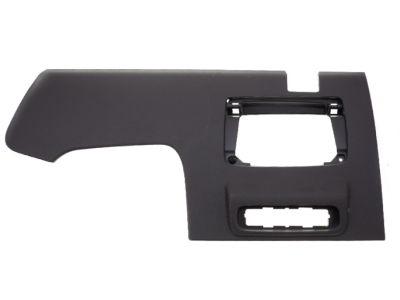
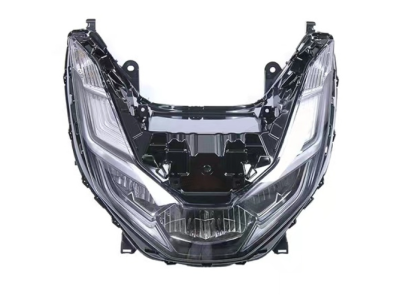
Put your parts
into production today
All information and uploads are secure and confidential.